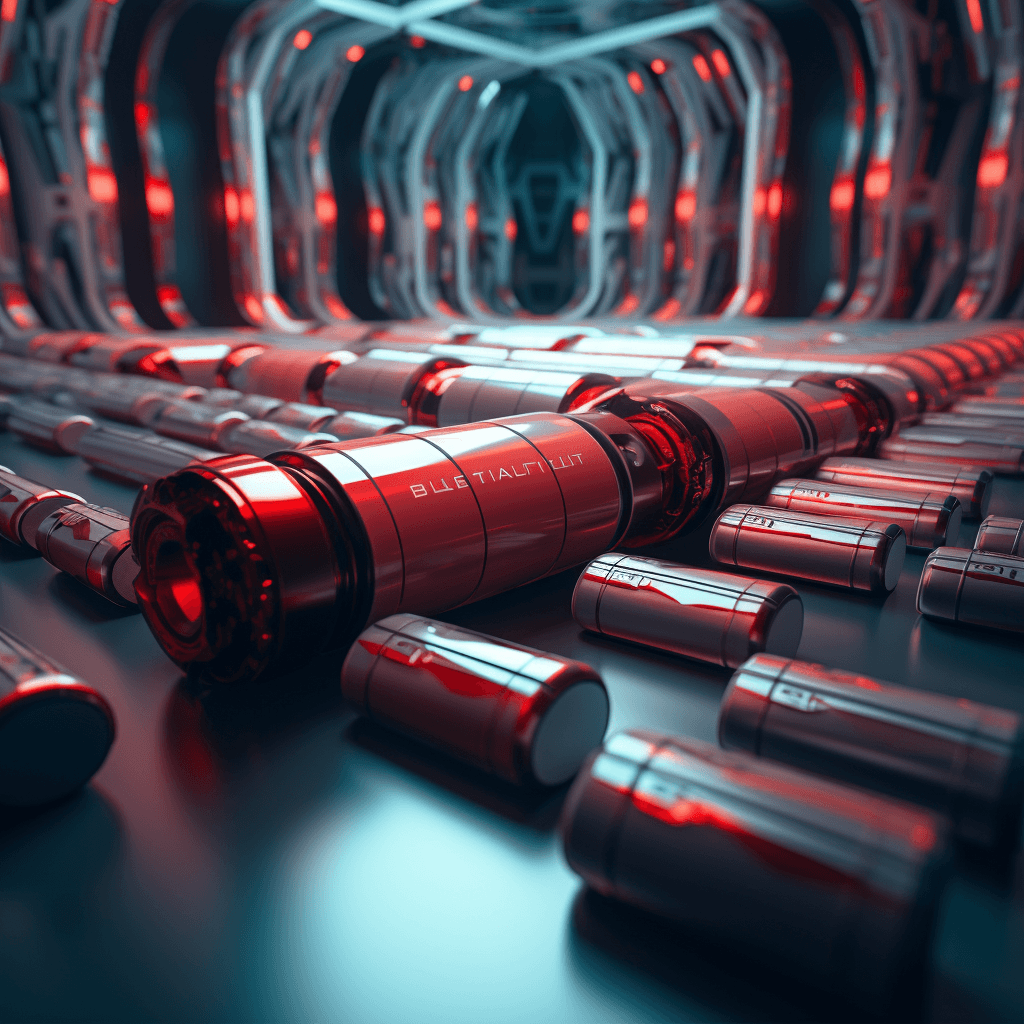
Die Batterieherstellung für die Zukunft optimieren
Aktie
Batterien spielen eine entscheidende Rolle in unserem täglichen Leben. Von Smartphones bis hin zu Elektrofahrzeugen wären unsere modernen technologischen Annehmlichkeiten ohne fortschrittliche Batteriesysteme nicht möglich. Da die Nachfrage nach Batterien steigt, suchen Hersteller ständig nach Möglichkeiten, die Produktion zu optimieren, um die Leistung zu steigern, die Kosten zu senken und mit den Marktanforderungen Schritt zu halten.
Durch verbesserte Herstellungsprozesse, die Erforschung neuer Materialien und den Einsatz modernster Technologien kann die Batterieproduktion effizienter und umweltfreundlicher werden und Produkte mit verbesserter Leistungsfähigkeit hervorbringen. Dieser Artikel untersucht den aktuellen Stand der Batterieherstellung und Möglichkeiten zur Weiterentwicklung, um zukünftige Leistungsanforderungen zu erfüllen.
Aktuelle Methoden zur Batterieherstellung
Die meisten modernen Batterien basieren auf Lithium-Ionen-Technologie und bestehen aus Anode, Kathode, Elektrolyt und Separator. Gängige Anodenmaterialien sind Graphit und Silizium, während Kathoden typischerweise aus Lithiumverbindungen wie Lithiumkobaltoxid bestehen. Der Elektrolyt transportiert geladene Lithiumionen zwischen den Elektroden und erzeugt so Strom.
Bei der Herstellung von Lithium-Ionen-Batterien müssen Hersteller Produktionsprozesse wie Elektrodenherstellung, Zellmontage, Elektrolytbefüllung und Verpackung sorgfältig kontrollieren. Die Elektroden werden mithilfe von Verfahren wie Aufdampfen oder Mischen mit Bindemitteln mit aktiven Materialien beschichtet. Die Zellen werden durch abwechselndes Stapeln von Kathoden- und Anodenschichten mit dazwischenliegenden Separatoren zusammengesetzt. Der flüssige Elektrolyt wird anschließend in das versiegelte Batteriezellengehäuse eingespritzt.
Während der gesamten Fertigung werden Qualitätskontrollmaßnahmen durchgeführt. Die Zellen werden auf ihre elektrische Leistung geprüft, ihre Abmessungen gemessen und auf Defekte untersucht. Fortgeschrittene Analysetechniken wie die Röntgen-Computertomographie können ebenfalls zur Bewertung der inneren Batteriestruktur eingesetzt werden.
Verbesserungsbereiche in der Batterieherstellung
Obwohl sich die aktuellen Herstellungsverfahren im Laufe der Jahre deutlich verbessert haben, gibt es immer noch Bereiche, in denen Verbesserungen möglich sind:
- Reduzierung der Chargenvariabilität und Verbesserung der Produktkonsistenz
- Ertragssteigerung und Minimierung von Ausschuss/Abfall
- Verkürzung der Produktionszeiträume, um der wachsenden Marktnachfrage gerecht zu werden
- Senkung der Geräte- und Betriebskosten
- Maximierung der Batterieleistungsmerkmale wie Energiedichte, Lebensdauer und Sicherheit
Neue Fertigungsansätze können helfen, diese Schwachstellen zu beheben. Strategien wie Prozessmodellierung, Automatisierung und erweiterte Qualitätskontrolle können die Produktion optimieren. Die flexible Gestaltung von Anlagen und Arbeitsabläufen ermöglicht Herstellern einen schnellen Produktwechsel.
Neue Batteriechemie und -materialien
Ein wichtiger Aspekt der Batterieherstellung der nächsten Generation ist die Entwicklung neuer Chemikalien und Materialien. Lithium-Ionen-Batterien dominieren derzeit, es werden jedoch Alternativen erforscht, um diese Grenzen zu überwinden:
-
Lithium-Schwefel-Batterien bieten eine hohe theoretische Energiedichte und verwenden kostengünstigen Schwefel an der Kathode. Es bestehen jedoch weiterhin Herausforderungen bei der Optimierung der Morphologie und der Verhinderung der Kathodenauflösung.
-
Lithium-Luft-Batterien nutzen Sauerstoff aus der Luft anstelle einer herkömmlichen Kathode. Dies ermöglicht eine außergewöhnlich hohe Energiedichte, allerdings müssen Probleme hinsichtlich Stabilität und Wiederverwendbarkeit gelöst werden.
-
Festkörper-Lithium-Ionen-Batterien ersetzen flüssige Elektrolyte durch feste Materialien, um Sicherheit und Energiedichte zu verbessern. Die Herstellungsprozesse müssen verfeinert werden, um dünne, gleichmäßige Festelektrolyte zu ermöglichen.
-
Multivalente Ionenbatterien mit Magnesium oder Aluminium an der Anode bieten Vorteile wie erhöhte Sicherheit und schnelleres Laden. Auf diese neuen chemischen Eigenschaften abgestimmte Herstellungsverfahren werden dabei eine wichtige Rolle spielen.
Durch die Beherrschung der Produktion neuartiger Batterien können Hersteller anspruchsvolle Leistungsanforderungen erfüllen.
Fortschrittliche Fertigungstechniken
Mehrere hochentwickelte Techniken, die heute zur Verfügung stehen, können dazu beitragen, die Batterieherstellung zu verbessern:
-
Die additive Fertigung mittels 3D-Druck ermöglicht eine größere Designflexibilität. Sie ermöglicht schnelles Prototyping und die Produktion komplexer oder optimierter Batteriekomponenten in Kleinserien.
-
Inline-Überwachungstools wie industrielle Bildverarbeitung verfolgen Batterien durch die Produktion und erkennen automatisch Fehler. Dies verbessert die Qualitätskontrolle und reduziert den Ausschuss.
-
Laserbasierte Verfahren ermöglichen das präzise Schneiden, Bohren, Schweißen und Strukturmodifizieren von Batteriematerialien im kleinen Maßstab. Laser finden in der Batterieherstellung zunehmend Anwendung.
-
Die nanoskalige Oberflächentechnik modifiziert Batteriematerialien auf mikroskopischer Ebene, um Eigenschaften wie Ladungstransfer und Ionentransport zu verbessern. Die kontrollierte Manipulation in solch kleinen Dimensionen ist entscheidend.
Die Anpassung dieser neuen Technologien an die Batterieherstellung wird in Zukunft zu erheblichen Verbesserungen der Produktleistung, -konsistenz und -anpassbarkeit führen.
Automatisierung und Robotik in der Batterieproduktion
Der verstärkte Einsatz von Automatisierung und Robotik bietet enormes Potenzial zur Optimierung der Batterieproduktion. Mit Spezialwerkzeugen ausgestattete Roboterarme können manuelle, repetitive Produktionsaufgaben mit höherer Geschwindigkeit, Präzision, Effizienz und Konsistenz übernehmen.
Fahrerlose Transportfahrzeuge (FTS) ermöglichen einen reibungslosen und fehlerfreien Materialtransport zwischen den Arbeitsstationen. Automatisierte Prüfsysteme prüfen Batterien sorgfältig auf Defekte. Durch die Minimierung des direkten menschlichen Eingriffs in die Fertigung wird die Variabilität reduziert und die Produktionsmengen können gesteigert werden.
Künstliche Intelligenz kann auch in der Produktionssteuerung, der Überwachung der Anlagenleistung, der Anpassung von Betriebsparametern und der Vorhersage des Wartungsbedarfs eingesetzt werden. Angesichts der steigenden Nachfrage nach Batterien werden automatisierte und robotergestützte Systeme zu unverzichtbaren Hilfsmitteln für eine wirtschaftliche Massenproduktion.
Qualitätskontrolle und Prüfung
Strenge Qualitätskontrollen und Tests gewährleisten optimale Batterieleistung, Sicherheit und Zuverlässigkeit. Während der gesamten Produktion werden Batterieproben in verschiedenen Phasen einer gründlichen analytischen Charakterisierung und Bewertung unterzogen.
Standardtests bewerten wichtige Kennzahlen wie Spannung, Kapazität, Impedanz, Leistungsfähigkeit, Zyklenlebensdauer und Temperaturstabilität. Umwelttests setzen Batterien Belastungen wie Feuchtigkeit, Vibrationen und Stößen aus, um ihre Widerstandsfähigkeit zu bestätigen. Bei Missbrauchstests werden Batterien gezielt beschädigt, um Ausfallarten und Sicherheitsreserven zu ermitteln.
Modernste Anlagen ermöglichen die Bewertung von Batterien unter präzise kontrollierten Bedingungen. Die Einhaltung strenger Qualitätsstandards durch umfassende Tests und Analysen ist für die Markteinführung verbraucherfertiger Produkte unerlässlich.
Nachhaltige und umweltfreundliche Herstellung
Angesichts der zunehmenden Besorgnis über die Umweltauswirkungen gewinnen nachhaltige Herstellungsverfahren in der Batterieindustrie zunehmend an Bedeutung. Dazu gehören die Minimierung von Abfällen, die effiziente Nutzung von Ressourcen, die Reduzierung von Emissionen, das Recycling von Materialien und die Gewährleistung der Arbeitssicherheit.
Verbesserungen der Produktionsprozesse in Verbindung mit einem verstärkten Einsatz von Automatisierung/Robotik schonen Ressourcen und sorgen für eine sauberere Arbeitsumgebung. Einige neue Batteriechemikalien verwenden reichlich vorhandene, ungiftige Materialien. Neu entwickelte wasserbasierte Herstellungsverfahren vermeiden gefährliche Lösungsmittel.
Auch das Recycling von Batteriematerialien wie Kobalt und Lithium zurück in die Produktionskreisläufe wird unerlässlich. Durch die Berücksichtigung ökologischer Aspekte kann die Batterieherstellung ihren ökologischen Fußabdruck verringern. Dies wird in Zukunft immer wichtiger.
Zukunftsaussichten für die Batterieherstellung
Der Bereich der Batterieherstellung steht an der Schwelle zu großen Veränderungen, die durch dringende Marktanforderungen, bahnbrechende Technologien und Materialien, automatisierte und optimierte Produktion sowie Nachhaltigkeitsbedenken vorangetrieben werden.
Da Elektrofahrzeuge und Energiespeicherung für unsere Energiezukunft von entscheidender Bedeutung sind, muss die Batterieproduktionskapazität drastisch gesteigert und gleichzeitig eine bessere Leistung zu niedrigeren Preisen erzielt werden. Bahnbrechende Fertigungsfortschritte in Bereichen wie additiven Verfahren, fortschrittlicher Qualitätskontrolle und Recycling werden zum Erreichen dieser Ziele beitragen.
Auch die Nutzung von Techniken aus Parallelbranchen wie der Halbleiterfertigung kann den Fortschritt beschleunigen. Um den zukünftigen Energiespeicherbedarf zu decken, muss die Batterieproduktion letztlich deutlich effizienter, flexibler, volumenstärker und wirtschaftlicher werden und gleichzeitig hohe Qualitätsstandards einhalten. Kontinuierliche Innovationen zur Erreichung dieser Ziele bieten hervorragende Aussichten, diesen wichtigen Sektor zu transformieren.