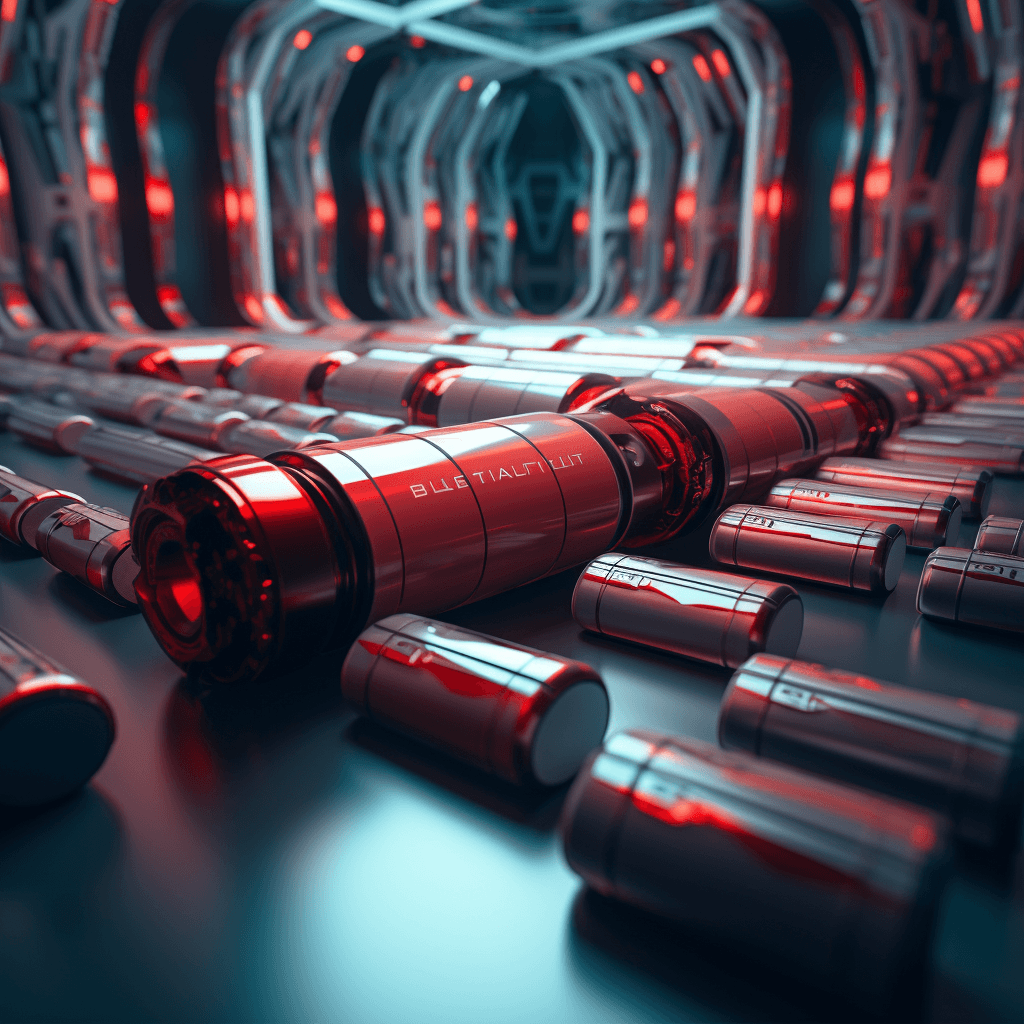
Suralimenter la fabrication de batteries pour l'avenir
Partager
Les batteries jouent un rôle crucial dans notre quotidien. Des smartphones aux véhicules électriques, nos technologies modernes ne seraient pas possibles sans des systèmes de batteries performants. Face à la demande croissante de batteries, les fabricants cherchent constamment à optimiser leur production pour accroître les performances, réduire les coûts et répondre aux besoins du marché.
En améliorant les procédés de fabrication, en explorant de nouveaux matériaux et en adoptant des technologies de pointe, la production de batteries peut devenir plus efficace, plus respectueuse de l'environnement et offrir des produits aux performances améliorées. Cet article examine l'état actuel de la fabrication des batteries et les possibilités de progrès dans ce domaine pour répondre aux exigences de performance futures.
Méthodes actuelles de fabrication de batteries
La plupart des batteries modernes utilisent la technologie lithium-ion et se composent d'une anode, d'une cathode, d'un électrolyte et d'un séparateur. Les anodes les plus courantes sont le graphite et le silicium, tandis que les cathodes sont généralement constituées de composés de lithium comme l'oxyde de lithium-cobalt. L'électrolyte transporte les ions lithium chargés entre les électrodes, générant ainsi de l'électricité.
Pour produire des batteries lithium-ion, les fabricants doivent contrôler rigoureusement les processus de production, tels que la fabrication des électrodes, l'assemblage des cellules, le remplissage de l'électrolyte et le conditionnement. Les électrodes sont recouvertes de matériaux actifs par des techniques telles que le dépôt en phase vapeur ou le mélange avec des liants. Les cellules sont assemblées par empilement alterné de couches de cathode et d'anode, séparées par des séparateurs. L'électrolyte liquide est ensuite injecté dans le boîtier de la cellule, qui est ensuite scellé.
Des contrôles qualité sont mis en œuvre tout au long de la fabrication. Les cellules sont testées pour leurs performances électriques, mesurées pour leurs dimensions physiques et inspectées pour détecter tout défaut. Des techniques d'analyse avancées comme la tomodensitométrie (TDM) peuvent également être utilisées pour évaluer la structure interne des batteries.
Domaines d'amélioration dans la fabrication des batteries
Bien que les méthodes de fabrication actuelles se soient considérablement améliorées au fil des ans, il existe encore des domaines d’amélioration potentielle :
- Réduire la variabilité d'un lot à l'autre et améliorer la cohérence des produits
- Augmenter le rendement et minimiser les rebuts/déchets
- Raccourcir les délais de production pour répondre à la demande croissante du marché
- Réduire les coûts d'équipement et d'exploitation
- Optimiser les attributs de performance de la batterie tels que la densité énergétique, la durée de vie du cycle et la sécurité
De nouvelles approches de fabrication peuvent contribuer à résoudre ces problèmes. Des stratégies telles que la modélisation des processus, l'automatisation et le contrôle qualité avancé peuvent optimiser la production. Concevoir des équipements et des flux de travail flexibles permet aux fabricants de passer rapidement d'un produit à l'autre.
Chimies et matériaux émergents pour les batteries
Un aspect important de la fabrication de batteries de nouvelle génération réside dans le développement de nouvelles compositions chimiques et de nouveaux matériaux. Les batteries lithium-ion dominent actuellement le marché, mais des alternatives sont étudiées pour dépasser ces limites :
-
Les batteries lithium-soufre offrent une densité énergétique théorique élevée et utilisent du soufre peu coûteux à la cathode. Cependant, des défis subsistent quant à l'optimisation de la morphologie et à la prévention de la dissolution de la cathode.
-
Les batteries lithium-air utilisent l'oxygène de l'air au lieu d'une cathode traditionnelle. Cela permet d'obtenir une densité énergétique exceptionnellement élevée, mais des problèmes de stabilité et de réutilisation doivent être résolus.
-
Les batteries lithium-ion à l'état solide remplacent les électrolytes liquides par des matériaux solides afin d'améliorer la sécurité et la densité énergétique. Les procédés de fabrication doivent être perfectionnés pour permettre l'obtention d'électrolytes solides fins et uniformes.
-
Les batteries ioniques multivalentes utilisant du magnésium ou de l'aluminium à l'anode offrent des avantages tels qu'une sécurité accrue et une charge plus rapide. Des méthodes de fabrication adaptées à ces nouvelles compositions chimiques seront essentielles.
La maîtrise de la production de nouvelles batteries permettra aux fabricants de répondre à des exigences de performance exigeantes.
Techniques de fabrication avancées
Plusieurs techniques sophistiquées disponibles aujourd’hui peuvent aider à améliorer la fabrication des batteries :
-
La fabrication additive par impression 3D offre une plus grande flexibilité de conception. Elle permet le prototypage rapide et la production en petites séries de composants de batterie complexes ou optimisés.
-
Des outils de surveillance en ligne, comme la vision industrielle, suivent les batteries tout au long de la production et détectent automatiquement les défauts. Cela améliore le contrôle qualité et réduit les déchets.
-
Les procédés laser permettent de découper, percer, souder et modifier structurellement les matériaux des batteries avec précision, à petite échelle. Les lasers trouvent de plus en plus d'applications dans la fabrication des batteries.
-
L'ingénierie de surface à l'échelle nanométrique modifie les matériaux des batteries à l'échelle microscopique afin d'améliorer leurs propriétés telles que le transfert de charge et le transport des ions. Une manipulation contrôlée à des dimensions aussi réduites est cruciale.
L’adaptation de ces types de technologies émergentes à la fabrication de batteries entraînera des améliorations significatives des performances, de la cohérence et de la personnalisation des produits à l’avenir.
Automatisation et robotique dans la production de batteries
L'automatisation et la robotique, en pleine expansion, offrent un potentiel considérable pour optimiser la fabrication des batteries. Des bras robotisés équipés d'outils spécialisés peuvent prendre en charge les tâches de production manuelles et répétitives avec une rapidité, une précision, une efficacité et une régularité accrues.
Les véhicules à guidage automatique (VGA) transportent les matériaux sans problème entre les postes de travail. Les systèmes d'inspection automatisés examinent minutieusement les batteries pour détecter d'éventuels défauts. En minimisant l'intervention humaine directe dans la fabrication, la variabilité est réduite et les volumes de production peuvent être augmentés.
L'intelligence artificielle peut également être appliquée au contrôle de la production, à la surveillance des performances des équipements, à l'ajustement des paramètres de fonctionnement et à la prévision des besoins de maintenance. Face à la demande croissante de batteries, les systèmes automatisés et robotisés deviendront des atouts essentiels pour une production économique en grande série.
Contrôle de la qualité et tests
Des contrôles qualité et des tests rigoureux garantissent des performances, une sécurité et une fiabilité optimales des batteries. Tout au long de la production, des échantillons de batteries sont soumis à une caractérisation et une évaluation analytiques approfondies à différents stades.
Les tests standard évaluent des paramètres clés tels que la tension, la capacité, l'impédance, la puissance, la durée de vie et la stabilité thermique. Les tests environnementaux exposent les batteries à des contraintes telles que l'humidité, les vibrations et les chocs pour confirmer leur résilience. Les tests de résistance aux chocs endommagent délibérément les batteries afin de comprendre les modes de défaillance et les marges de sécurité.
Des installations de pointe permettent d'évaluer les batteries dans des conditions contrôlées avec précision. Le respect de normes de qualité rigoureuses grâce à des tests et analyses complets est essentiel pour commercialiser des produits prêts à être utilisés par les consommateurs.
Fabrication durable et respectueuse de l'environnement
Face aux préoccupations croissantes concernant les impacts environnementaux, les pratiques de fabrication durables deviennent une priorité croissante dans l'industrie des batteries. Elles incluent la réduction des déchets, l'utilisation efficace des ressources, la réduction des émissions, le recyclage des matériaux et la sécurité des travailleurs.
L'amélioration des processus de production, associée à un recours accru à l'automatisation et à la robotique, préserve les ressources et offre un environnement de travail plus propre. Certaines nouvelles compositions chimiques de batteries utilisent des matériaux abondants et non toxiques. De nouvelles techniques de fabrication à base d'eau évitent l'utilisation de solvants dangereux.
Le recyclage des matériaux des batteries, comme le cobalt et le lithium, dans les circuits de production deviendra également essentiel. En prenant en compte les considérations environnementales, la fabrication des batteries peut limiter son empreinte écologique. Cet aspect ne fera que gagner en importance à l'avenir.
Perspectives d'avenir pour la fabrication de batteries
Le secteur de la fabrication de batteries est à l’aube de changements majeurs motivés par les demandes urgentes du marché, les technologies et matériaux disruptifs, la production automatisée et optimisée et les préoccupations en matière de durabilité.
Les véhicules électriques et le stockage d'énergie étant considérés comme essentiels à notre avenir énergétique, la capacité de production de batteries doit considérablement augmenter, tout en offrant de meilleures performances à des prix plus bas. Des avancées technologiques majeures dans des domaines tels que les procédés additifs, le contrôle qualité avancé et le recyclage seront essentielles pour atteindre ces objectifs.
L'exploitation de techniques issues d'industries parallèles, comme la fabrication de semi-conducteurs, peut également accélérer le progrès. À terme, pour répondre aux besoins futurs en matière de stockage d'énergie, il faudra que la fabrication de batteries devienne nettement plus efficace, flexible, en grande série et économique, tout en maintenant des normes de qualité rigoureuses. L'innovation continue en vue de ces objectifs offre d'excellentes perspectives de transformation de ce secteur vital.